Quality & Efficiency
Rigorous quality assurance is at the heart of a successful intralogistics project.
We at Arete know that and offer a commitment to both quality and continuous improvement.
Quality Assurance
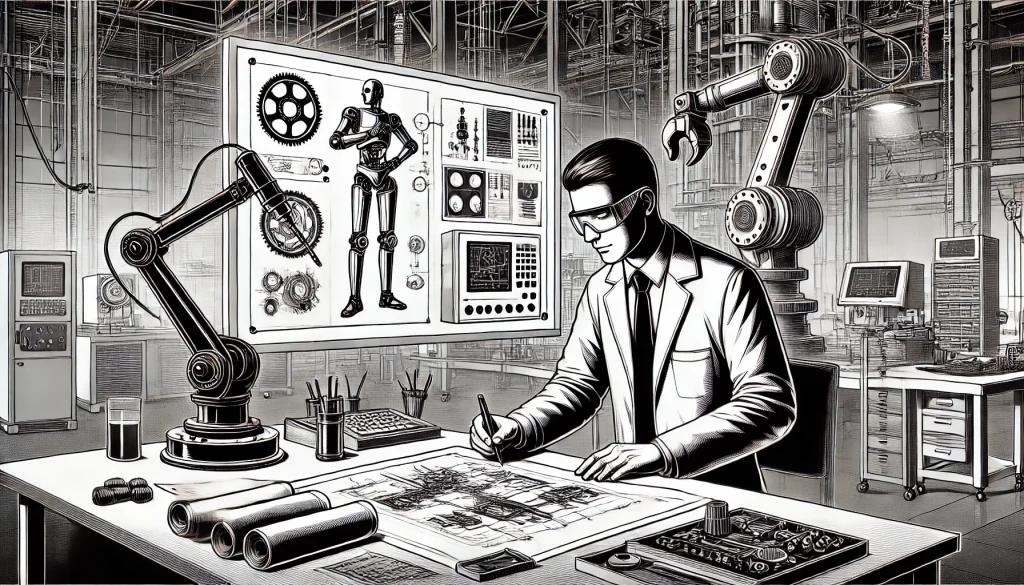
A project without quality assurance is like a building without a foundation – eventually, it will collapse under the weight of unresolved issues.
Arete ensures that all system functionalities and specifications meet the highest industry standards and client expectations by conducting thorough testing, validation, and audits throughout the entire project lifecycle and beyond that.
To prevent costly errors and operational disruptions Arete’s QA services ensure that all systems are thoroughly tested and validated before going live.
By conducting quality assurance plans, requirement analysis, thorough specification reviews, testing and validation reports, performance monitoring tools, issue logs, resolution reports and final quality audits and certifications Arete ensures that your project meets the highest industry standards in terms of quality assurance.
Process Optimization
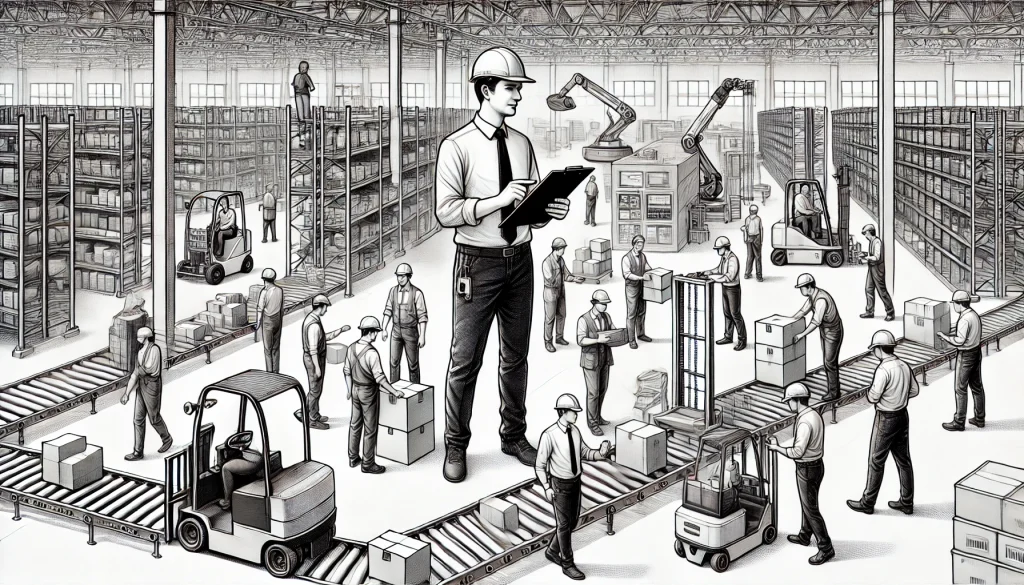
Optimizing processes allows businesses to do more with less, ensuring resources are utilized effectively without compromising quality.
Existing operational or systemic processes and workflows are evaluated by Arete to identify inefficiencies or bottlenecks and thus recommend solutions to improve throughput, productivity and overall operational efficiency.
Results are captured in custom process optimization reports and an implementation plan for process or system related changes is then conducted with the client and vendors.
Performance Analysis
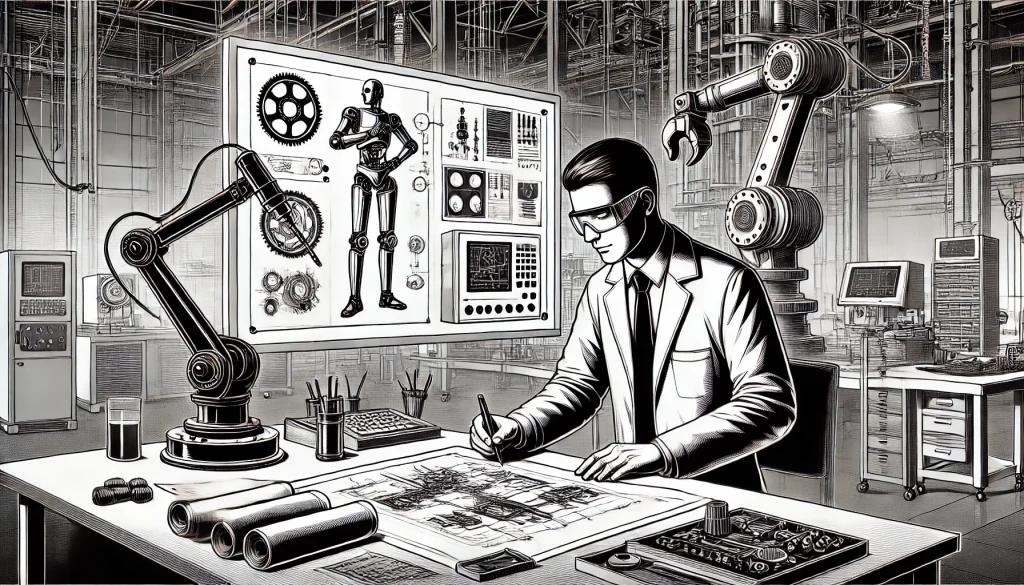
Decision-making relies on guesswork, without performance analysis, while data-driven insights offer the key to informed improvements.
Simulations and analysis of the proposed or already installed system are conducted to validate its performance under various conditions, including peak loads, to ensure it can meet operational demands.
An early performance analysis prevents bottlenecks or system limitations after go-live, ensuring the system is designed to meet the client’s expectations.
Arete conducts periodic performance analysis reports, which identify bottlenecks and underperforming areas in an early stage of the project and provides a performance improvement roadmap to the client and vendors.
Continuous Improvement
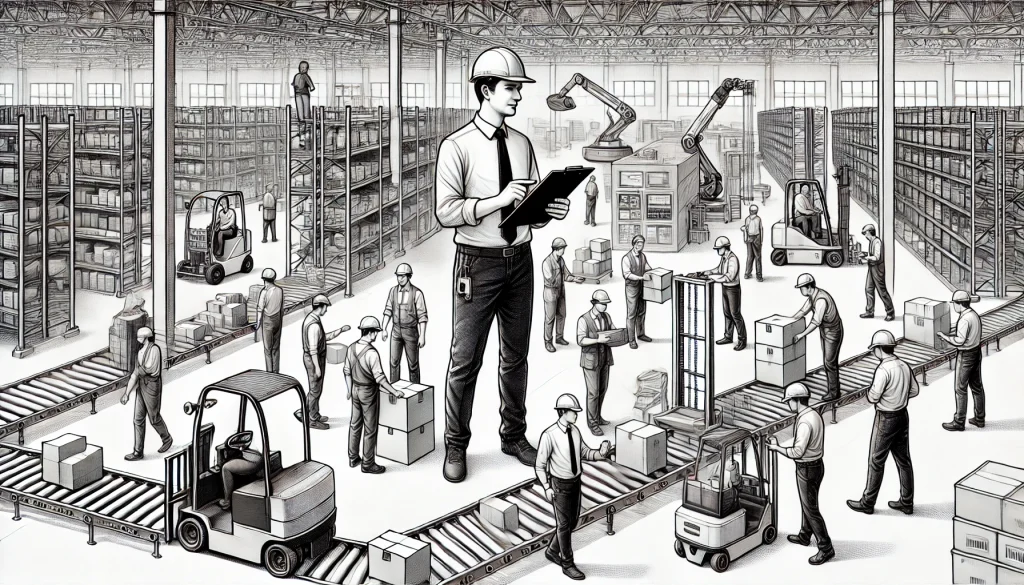
Without continuous improvement, organizations risk stagnation, while those that embrace it stay competitive and forward-thinking.
To make sure the system remains efficient and adaptable over time, having a continuous improvement framework and roadmap is crucial after going live.
Arete supports in implementing a structured continuous improvement model, based on regular performance review reports and user feedback (future change requests, minor bugs, etc.).
This roadmap’s goal is to regularly review and refine the systems, processes, and workflows in order to increase efficiency, reduce costs, and improve overall performance.
Design Phase
The bare bones of a successful intralogistics solutions lie in the project design itself. Our consulting goes from:
- Elaborate Requirement Analysis
We work closely with your team to understand your unique needs, ensuring that all functional and non-functional requirements are accurately captured and addressed. - Risk Assessment and Mitigation
The identification of potential risks in the design phase early enough may develop appropriate mitigation strategies, which can reduce the likelihood of expensive issues further down the project. - System Specification and Design Reviews
Our professionals perform detailed system specification and design documentation reviews to ensure that each element is in compliance with industry best practice and your specific operational goals.
Implementation & Delivery
Delivery is where the plans are implemented. The quality assurance services we offer during this stage include:
- Supplier coordination and oversight:
We maintain relations with the equipment suppliers and software vendors in order to ensure that all items delivered are indeed per the agreed-upon specifications and quality standards. - Factory Acceptance Testing (FAT):
This is one of the areas that our team looks into with much concern as it will ensure that the components of the system are performing well before being shipped to your site, thus identifying problems early enough. - Host Communication, Sandbox & Integration:
We supervise joint test phases such as Host Communication Tests, Sandbox Tests and Integration Tests, coordinating with each stakeholder so that testing is done methodically and, most importantly, problems are identified and resolved without delay. - Creation of test plans:
We develop comprehensive test plans based on your specific needs, taking into consideration all aspects of the system, which in turn allows us to conduct detailed tests on functionality, performance, and reliability. - Installation and Integration Supervision:
All installation and integration processes are supervised on behalf of our customers, ensuring proper implementation of all the systems with minimal downtime or interruption to regular services. - Execution of tests
We carry out thorough testing according to the test plans, ensuring that every aspect of the system is evaluated for performance, reliability, and compliance with specifications.
Ramp-Up & Support
The ramp-up phase is critical since it leads to the shift from project implementation to a fully operational state. For this stage, we provide the following:
- Site Acceptance Testing (SAT)/Customer Integration Testing (CIT)
The whole system works as expected in your operational environment, and this is ensured through thorough SAT (or customer integration testing) and commissioning activities. We will create the test plans for you and support in the execution of those. - Performance Monitoring and Optimization
Arete continuously monitors system performance since its installation during the ramp-up phase, optimizing areas to enhance efficiency and productivity and provides the right tool for that analysis. - Training and Support
The staff of your company will be fully trained by us so that they are fully competent in operating and maintaining the new systems. Ongoing support also ensures that any arising problems can be addressed promptly.